IO Links
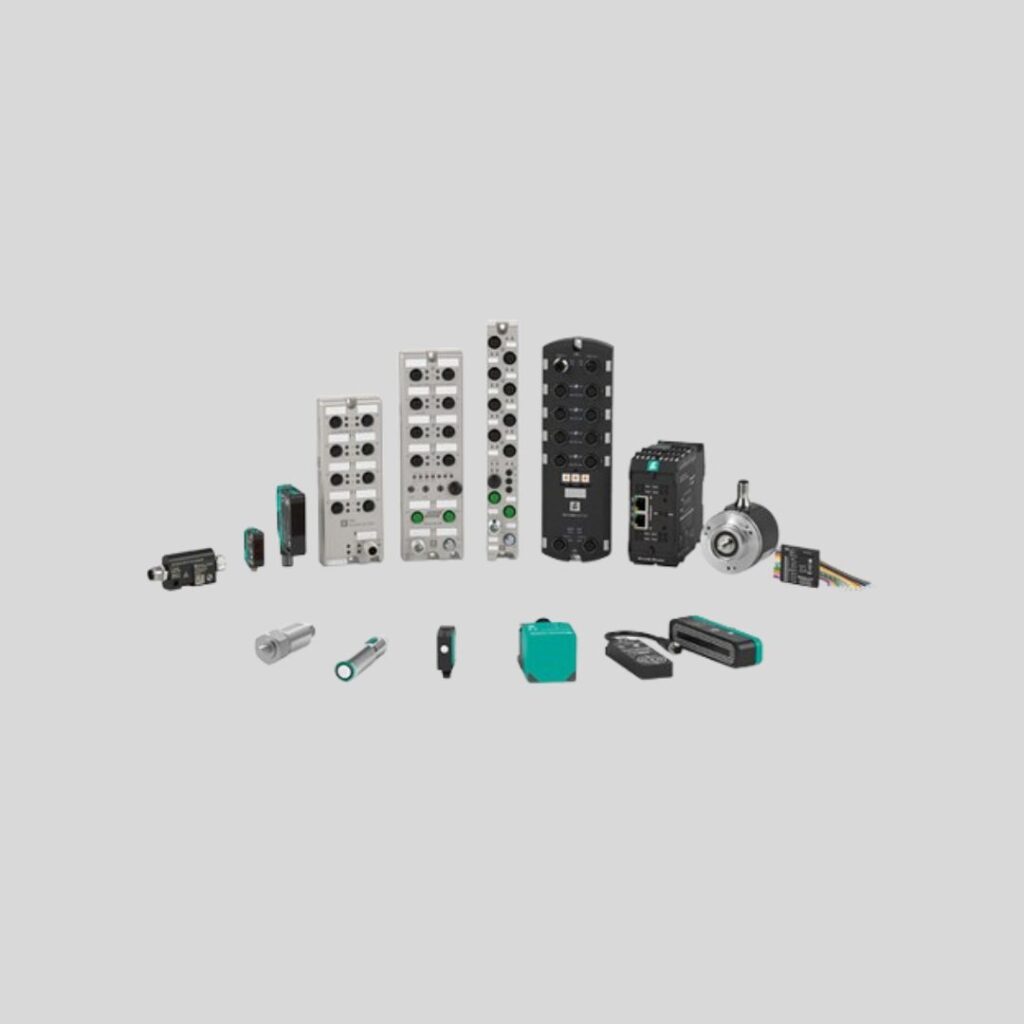
Understanding IO Links: Revolutionising Industrial Communication
Efficient communication among devices is crucial in the current dynamic industrial landscape to maximise efficiency and augment production. IO Link is among the most promising answers to this problem. The benefits, uses, and potential effects of IO Link technology on industrial automation are examined in this article.
What is IO Link?
In an industrial context, IO Link is an open standard communication protocol that makes it easier to connect sensors, actuators, and controllers. This technology, which was created by the IO-Link Consortium, facilitates seamless data integration and transfer by acting as a bridge between field devices and higher-level systems.
Key Features of IO Link
Point-to-Point Communication:
By creating a direct link between a master device and several I/O devices, IO Link enables efficient communication without the need for intricate wiring.
Device configuration and diagnosis:
Device configuration can be done remotely via IO Link, making maintenance and troubleshooting simpler. This increases overall efficiency and decreases downtime.
Standardization:
Since IO Link is an open standard, devices made by different manufacturers can work together because it is manufacturer-independent.
Data Exchange:
In addition to binary signals, IO Link facilitates the transfer of process and diagnostic data, offering a more complete picture of the status of the device.
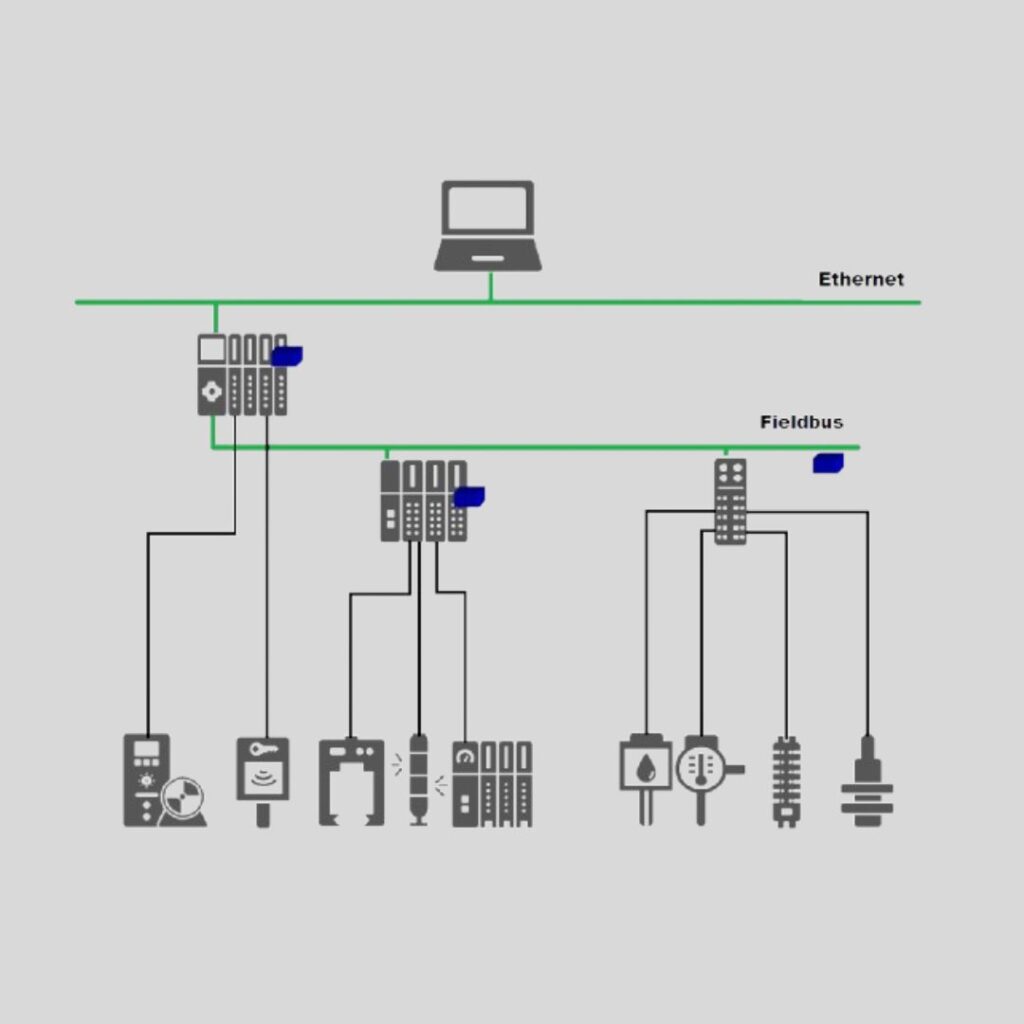
IO Link Brand
- Balluff
- Festo
- IFM Electronic
- Lenze
- Omron
- Phoenix Contact
- Siemens
Advantages of IO Link
Enhanced Data Transparency:
Real-time data gathering from sensors and actuators is made possible by IO Link. Better performance monitoring of the equipment is made possible by this transparency, which can also inspire predictive maintenance plans that lower the likelihood of unplanned breakdowns.
Simplified Wiring:
The complexity of wiring systems is decreased by IO Link’s point-to-point architecture. Installation and maintenance become easier and more cost-effective with fewer cables and connectors needed.
Flexibility and Scalability:
It is easy to adjust IO Link systems to changing industrial needs. Large-scale network overhauls are not necessary for the integration of new devices, enabling scalable solutions that expand along with the needs of the company.
Cost Efficiency:
IO Link lowers overall industrial automation costs by improving operational effectiveness and reducing wire expenditures. The requirement for on-site interventions is further decreased by the capability to diagnose and setup equipment remotely.
Applications of IO Link
Factory Automation:
IO Link is used in manufacturing settings to link a range of devices, including actuators, control systems, and sensors. This connection increases productivity overall, improves data flow, and streamlines operations.
Process Automation:
Process control and precise monitoring are made possible by IO Link in the chemical and pharmaceutical industries. In order to guarantee ideal process conditions, sensors can transmit data in real time about temperature, pressure, and other important factors.
Robotics:
Robots that have devices that support IO Link are able to connect with their control systems efficiently. Through real-time modifications depending on feedback, this communication enhances the precision and efficiency of robotic jobs.
Logistics and Material Handling:
Material handling systems can be optimised via IO Link in logistics and warehouses. Conveyor and sorting system sensors supply vital information that enables effective product handling and routing.
The Future of IO Link in Industry 4.0
With the shift of industries to Industry 4.0, data-driven decision-making and connectivity become critical. Because it facilitates smooth connectivity across systems, cloud apps, and devices, IO Link is essential to this transition.
Integration with IoT:
Processes in industry are changing as a result of the Internet of Things. Because it makes it easier for sensors and actuators to communicate with cloud-based platforms, IO Link acts as a basis for IoT integration. Deeper insights into operational efficiency can be gained through enhanced analytics and remote monitoring made possible by this combination.
Smart Manufacturing:
By allowing devices to share data intelligently, IO Link improves automation in the field of smart manufacturing. Advanced manufacturing methods, such adaptive production systems that change in real time in response to data inputs, are supported by this capacity.
Increased Customization:
Manufacturers can provide their customers with more individualised solutions with IO Link. Tailored applications that address particular operational needs are made possible by the remote configuration of equipment and the real-time data collection capabilities.
Challenges and Considerations:
Even while IO Link has many benefits, there are drawbacks to take into account. To fully utilise IO Link systems, equipment from various manufacturers must be compatible with one another. Data integrity must also be safeguarded by security measures, particularly as systems get increasingly interconnected.
With its improved flexibility, streamlined wiring, and increased data openness, IO Link is completely changing the way industrial devices communicate. Because of its wide range of uses, it is an essential part of contemporary automation systems. IO Link will be essential in promoting efficiency and innovation as industries adopt Industry 4.0 and IoT integration.
Businesses can use IO Link to optimise operations and maintain competitiveness in an increasingly complex industrial environment by knowing its advantages and applications. When it comes to robots, process control, or factory automation, IO Link is a crucial component that makes smart, connected manufacturing possible.